Unique Advantages and Benefits of Thick Film Heaters
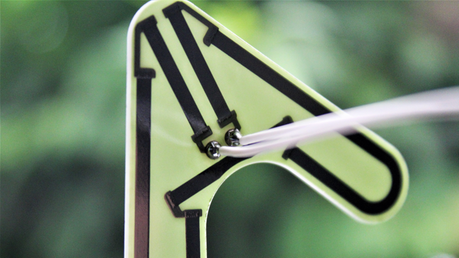
For surface heating, there are other choices of heaters. Heatron provides Flexible Silicon Heaters, Kapton® Polyimide Etch Foil heaters, and Etched Mica Heaters. The question is why choose Thick Film Heaters as your heating solution? Below lists and explains the unique advantages and benefits that TFHs can offer, and sometimes, cannot be replaced by other forms of surface heaters.
1) Heating Pattern: TFHs are made with screen printed heating traces which can be tailored to applications to deliver even heat for thermal uniformity across a surface, or different power densities (heat) in different areas,e., more power can be targeted in certain areas to meet the needs of the application. This is done by the combination of three factors: (1) the designing pattern of heating traces that intensify heating at cold spots or areas on the surface; for example, multiple independent heat zones can be designed into one heater; (2) formulating the pastes with a wide resistance range to deliver sufficient wattage, (3) adjusting printing width and depth to supplement the resistivity of the paste. The ending result is the capability of TFHs to apply heat with very predictable heat distribution across the surface or just in certain areas, uniform or concentrated on cold spots, and to accommodate the features of surface area and optimize the amount of heat transfer by virtue of conduction.
2) Odd Form Factors: Unlimited unusual heater shapes and geometry fit targeted areas for unique heating patterns. The intention is to fit custom profiles or areas. At Heatron, ceramic (Al2O3 and AlN), aluminum, and stainless-steel substrates are cut with precision lasers into almost any 2-dimensional shapes, a great solution to situations where custom form factors exist but other heaters will not fit or do not perform effectively. Heatron’s sales and application team is available to understand customer’s applications and design a TFH that best fits the project specifications.
3) Design Versatility: Versatility in the design of TFHs, shapes and heating distribution, enables value engineering to shorten development cycle and reduce costs.
4) Low Profile and Small Footprint: The most distinguishing characteristic of TFHs is its low profile and its ability to be made with very small dimensions. As thin as 0.010”, the THFs minimize the space requirements and are ideally suitable for thermal coupling to flat heat sinks, circuit boards and bulk heads, etc. This is a clear advantage when compared to bulky wire wound type heaters such as flexible silicone laminated heaters, as the wires must be either very long or the AWG of the wire has to be very small. TFHs overcome the space issue by selecting an ink of a particular resistivity value from a wide range.
5) Substrates Choice: Various substrate materials can be utilized to be compatible with heated objects and environments under which TFHs operate. The ceramic substrates have excellent corrosion resistance properties, stainless has moderate corrosion resistance, and aluminum offers a high resistance to corrosion once the surface oxide is formed. Thermal conductivity, which intrinsically is the heat transfer from heater to object, varies for different substrates. Stainless steel has the lowest value of about 15 W/mK and aluminum nitride (AlN) has the highest value up to 220 W/mK.
6) Light Weight: The TFH is thin and light weight, excellent for applications with a need for rapid heating and uniform temperature. The low mass also lowers energy consumption and boosts performances.
7) Low Thermal Mass or Heat Capacity: The low thermal mass is ideal for rapid thermal response or fast temperature cycling. Having a low heat capacity, the temperature can be increased quickly by using low amounts of energy.
8) Maximum Heat Transfer: Due to the direct surface contact, a TFH ensures efficient heat transfer via conduction through thermally stable substrates and precise resistance trace patterns.
9) No Electrical Complication: The printed pattern can reduce or eliminate potential electrical inductance and capacitance inherent in wound resistance wires. The inductance and capacitance currents may cause issues of nuisance ground-fault that is unacceptable.
10) High Operating Temperature: Ceramic TFHs have a maximum operating temperature up to 1832°F, such as Heatron’s high temperature ceramic TFHs (Al2O3 and AlN).
11) High Watt Density: Standard products range between about 20 W/in² and 40 W/in², but Heatron can provide 75 to 1000 W/in², depending on the substrates.
12) Corrosion Resistant: Ceramic TFHs have excellent corrosion resistance and perform well under corrosive conditions where acid and alkali solutions exist. Aluminum TFHs, after forming a layer of oxidation by gaseous acids present in the air which serves as a corrosion-resistant layer, can perform well in most corrosive environments. Stainless steel substrate can, however, tolerate only modest corrosions.
13) Long Life: The service life of TFHs can be very long if the application conditions are met according to instructions of operation. Heaters tend to last longer if the temperature is kept below its designed maximum temperature rating, as high temperatures accelerate deterioration of the heating traces, the dielectrics and protective layer.
For more information about the structure of Thick Film Heaters, the fabrication process, advantages of TFHs, applications in the industry, and what Heatron's Thick Film Heaters have to offer to you, download our complete Thick Film Heating guide. This full guide provided by Heatron will allow you to develop a better understanding about TFHs to assist you in finding the right one for your project(s).